The aerospace industry has been enthusiastic about composite materials and their use, as well as their disappointment. Composites have been used in jet aircraft for decades, but their design, manufacture, and post-processing have been treated the same as metals. Composites are a more difficult technology to design than metals because of their complexity. Because there is not much theory behind simulating or estimating the behaviour of composites, the same simple methods used for metals are applied to them. Fibre reinforced composites are directional by nature, whereas metals are omnidirectional, and all design methods are created for isotropic materials.
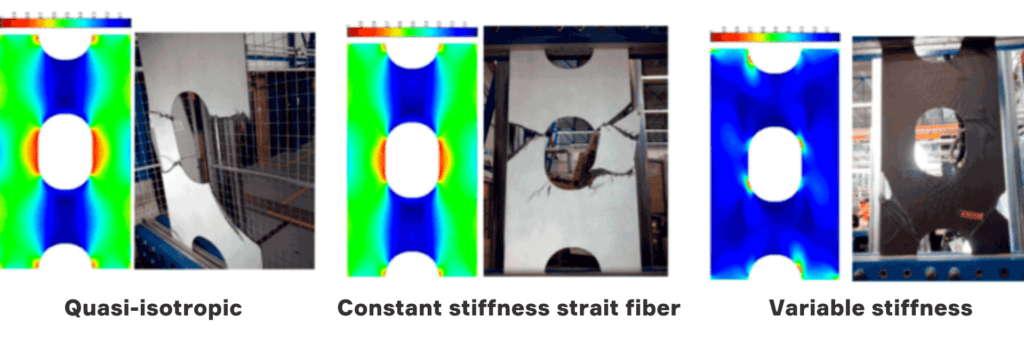
Why treating composites like isotropic materials is not a good idea
Engineers developed a quasi-isotropic composite material and then treated it as though it were isotropic. They layered stripes and fibers and textiles in all directions in order to simulate an isotropic material, and then applied the same procedures as those used on metals. However, this technique essentially negates the advantages of composites. Here are the values for both aluminium and continuous fiber reinforced polymer.
A laminate, a quasi-isotropic composite, is ten times as strong in one direction than it is in others, but the strength of laminate is only 300, which is less than that of aluminum. Yes, it is still lighter, but the trade-off is a mere 20-30% increase in strength instead of a tenfold increase.
There are, in addition to the cracks, delamination, slight damage, poor impact resistance, monitoring, maintenance, and other issues, a 20-30% bonus does not compensate for all the problems you encounter. Those in the composite industry are pessimistic because they think that quasi-isotropic design is the only method for creating composites, which is incorrect.
Understanding the benefits of Anisotropy – the key to design optimal composites
Mathematically speaking, when a structure is loaded, there is a response called stress at every point where the load is applied. And stress is a directional value; it is not a vector, but a tensor, which is more complex, but it is directional nonetheless.
The tensor operates on the idea that there is an internal resistance with a direction for each material point, and that material properties should therefore be concentrated on this direction. Only the properties of the material that resists in that direction are needed.
And you don’t need them in the opposite direction, or even just to the extent that the material resists in that one. The stress resistance pattern for isotropic material is uniform and spherical in all directions.
However, only one direction can be resisted by your material strength; the other directions are unnecessary. Thus, adjusting anisotropy at every material point, including orientation and ratio, enables the creation of structures that perfectly match responses.
There is still optimization in a traditional design paradigm, but it only affects the shape. Composites enable shape, internal structure, and property optimization, adding another level of optimization.
This dimension enables the construction of much more ideal structures in which the material behaves precisely in the desired directions and points. But that’s not how things are done in business today.
Generative design – How nature uses composites
Anisoprint worked on anisotropic media topology optimization and generative design, and the outcomes looked entirely different and more organic. Given that generative design and evolution employ similar methods, this is quite obvious.
It is comparable, but not exact. It is clear from this that they achieve similar results. Anisoprint wondered at this point: What if you looked at nature to find out what kinds of natural materials there are?
What are the components of natural evolutionary design, and how do they appear? Examples exist in nature, including the fibrous components found in grass and trees. Collagen fibres can be found in the skin and muscles of humans.
The fact that the method is universal in nature indicates that it is energy-efficient, which is crucial for evolution. And one more amusing fact: metals have been used by nature as building materials. Because it would require too much energy, nature has not yet discovered a way to use the metals that are present in the environment to build structures.
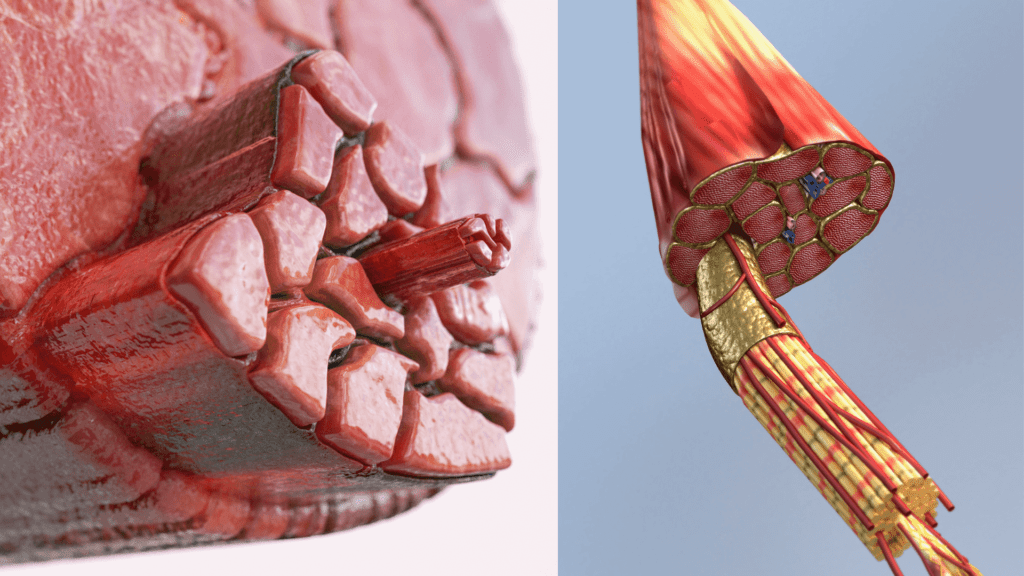
Building metal-free constructions with fiber reinforced composites
Metals require a lot of energy to process before being used to create something. We won’t use metals in the future because they are obviously not optimal and will soon become obsolete in favour of composites or composites with fibre reinforcement. There is already a trend in construction to use composite materials in place of metals.
Therefore, the process of evolution in nature differs slightly from the process of optimization that we do or can do. This is amusing because nature adapts to its environment. Each palm tree has its own DNA, allowing it to build itself, but it also adapts to its environment by building itself. These are also very fascinating things.
Humans occasionally use this tactic, but typically we imagine an environment, describe it, and then claim that “Our structure should work in this environment.”
The structure is then constructed, placed in the environment, but does not grow in an adaptive manner. That’s probably too far in the future, but eventually we’ll probably figure out how to make adoptive structures, and then we’ll move on. Although the composites design process may initially seem overwhelming, with a little work, it is possible to produce structures that are much more effective and efficient.
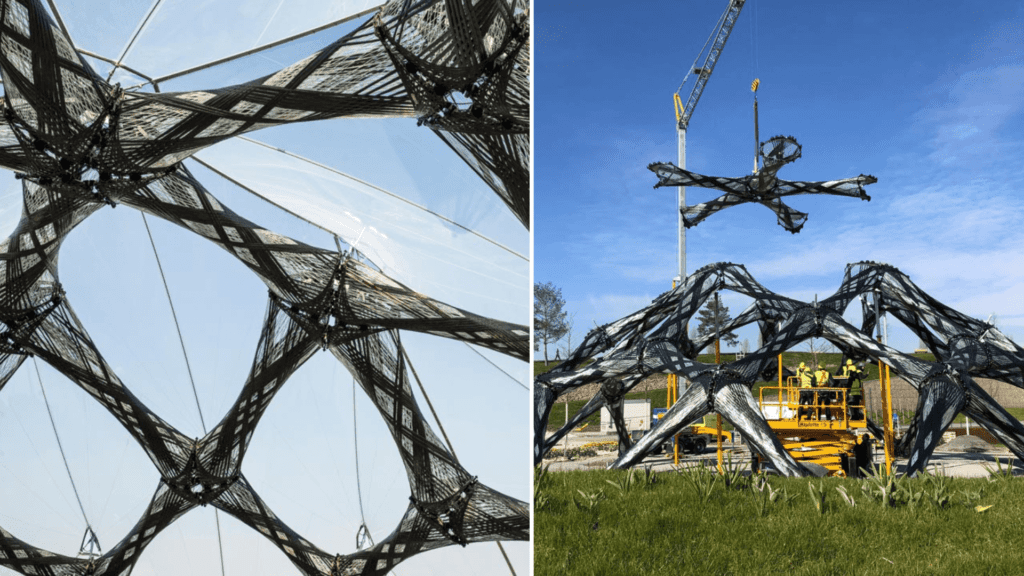
We can assist you in using composites to rethink your product design. Contact us today to see how our range of Anisoprint 3D printers can help your business.