The last several months have seen a significant increase in reports on coronaviruses in the medical 3D printing news. Masks, ventilators, valves, even the development of vaccines were all supported by 3D printing. However, the medical industry has always had a positive relationship with 3D printing, even before Covid-19 notably made headlines.
Basic external prostheses were the first to utilize 3D printing’s capacity to create specialized items catered to patients’ particular anatomical requirements. Then, as techniques and materials improved, 3D printed implants started to show up within the body. It was evident that 3D printed materials were suitable for medical devices, since people were moving around with exterior and internal 3D printed components that were a part of their bodies.
What else might be done better? What about an implant’s interior geometry, perhaps print a few trabecular structures with some porosity to aid osseointegration or a titanium implant is making a patient to walk abnormally since the meta implant itself lacks the elasticity of the bone it replaced.
There is, in fact, a method. The medical implant sector benefits from increased innovation and product development time when 3D printing is paired with novel materials, generative design, and topology optimization tools.
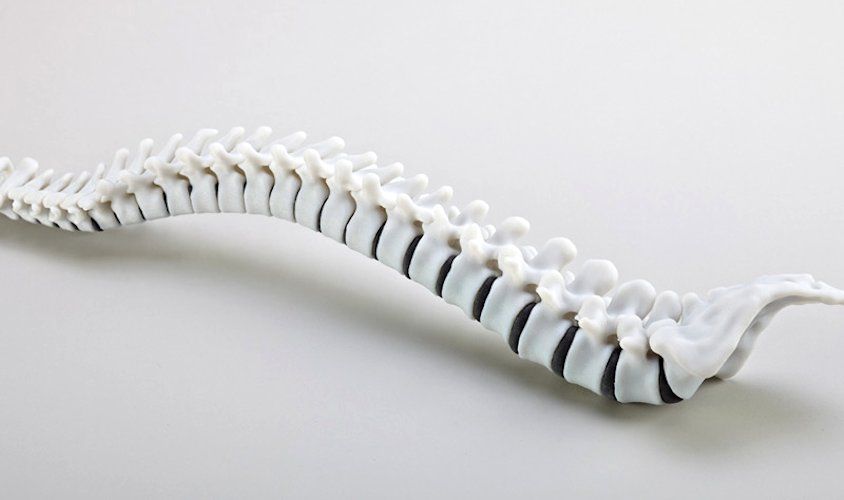
NuVasive – Topology Optimised Spine Implants
NuVasive, a US business that has been working on producing lightweight, stronger structures that enable better bone development inside the implant, is one company making improvements in the field of spinal implants (osseointegration).
NuVasive introduced the Modulus implant in 2017. With the support of 3D Systems’ Direct Metal Printing (DMP) technology and team of application experts, they were able to get from concept to market in only one year. Since then, the modulus has evolved from a single product to a whole implant product line, with each product topologically tuned to give the optimal combination of weight, strength, and X-ray detectability, allowing surgeons to monitor the implant’s integration with natural bone.
New Titanium for Printing
Of course, printing implants entails more than simply ensuring that it has the same form and volume as the object it is meant to replace, inserting it into a patient, and praying for the best. Aside from solid shape, several other factors influence osseointegration. The implant material itself is one such flaw. McMaster University researchers have been investigating the usage of Ti-5553 grade titanium for 3D printed implants. The majority of implants are presently manufactured using Ti64 powder feedstock… However, this may not be the ideal all-around implant material solution.
Ti-5553 is not commonly used in medical implants. It is most typically found in Russian fighter aircraft and helicopter constructions.
The advantage of Ti5553 is that it has a lower elastic modulus than Ti64, which should minimize stress-shielding once put in the patient. With this in mind, the researchers decided to compare the aerospace alloy to its biological equivalent, Ti64.
The researchers printed test specimens of both titanium alloys and then anodized them, altering the topology of the printed samples. On titanium samples, anodizing creates small surface characteristics known as nanopores and nanotubes. These topographical characteristics can help with bone bonding. When compared to the standard Ti64, the Ti5553 generated bigger tubes after anodizing. This suggests that Ti5553 is not only useful for printing, but it is also superior for osseointegration.
What Comes Next?
Although there has been much innovation in this subject, there is still more work to be done in terms of monitoring long-term advantages. After all, the field is still very young.
“Titanium 3D printed cages provide a peculiar geometry which optimises bone ingrowth profile, but this needs to be confirmed by further studies,” said Enrico Tessitore, deputy chairman of the Neurosurgical Unit at Geneva University Hospitals in an interview with Spinal News International.
His institute is now participating in a randomised investigation employing 3D manufactured interbody cages. “We perform a very early SPECT-CT scan in order to see if there is an early integration of these cages. Compared to PEEK cages, for example. 3D printing technology seems to promote fusion by facilitating ingrowth of bony cells from the endplates into the cage.” So the future looks promising for everyone who will require a spinal implant in the not-too-distant future.
3D printers are changing; new materials are being explored, and new software allows for more precise geometries. Most significantly, these processes are being evaluated and verified medically for use in assisting actual patients. And these workflows just include AM; they do not depict the entire picture. In the coming decade, robotic guided, augmented reality navigated surgical equipment will all play a role in enhancing spinal surgery.
We offer medical-grade 3D printing filaments at 3D APAC. Our filaments are of the highest quality and are made especially for the medical industry.
Please get in touch with us if you have any inquiries or wish to place an order.
We look forward to assisting you in developing your medical 3D printing.