The NASA EPSCoR award of $1.125 million is a partnership between UNO Biomechanics and Copper3D, a Chilean business that is a pioneer and worldwide leader in antimicrobial materials and uses for the 3D printing industry.
Scott Tarry, Ph.D., Director of NASA Nebraska EPSCoR, and his staff will provide logistical assistance for the initiative. Jorge Zuniga, Ph.D., UNO assistant professor and co-director of the Biomechanics Rehabilitation and Manufacturing Initiative, will lead the research team. (BRMI).
“In space, astronauts on long-term missions suffer from immune system dysregulation due to confinement, exposure to high radiation, and disturbed sleep cycles. Bacteria and viruses become more resistant in microgravity, which adds to the previous factor, making space missions of more than six months very risky,” explained Zuniga.
“It is extremely important to have new materials, tools, medical devices, and everyday objects with antimicrobial properties in space to prevent infection and to help keep astronauts healthy.”
Through this award capital, two novel antimicrobial materials will be created by Copper3D, then manufactured and evaluated for safety on Earth in a replica of the International Space Station’s (ISS) Additive Manufacturing Facility. The crew will get ready for the launch, operation, and return-to-Earth operations once the material’s safety has been confirmed.
In addition to developing test coupons and printed approximations of the ultimate in-space devices, UNO Biomechanics will collaborate with NASA and the 3D printer maker Made in Space to carry out post-testing of the antimicrobial efficiency on Earth.
“The current logistical model relies on continual resupply missions from Earth to the ISS, which is unsustainable for long duration space missions,” said Alex Blanchard, project lead for In-Space Manufacturing Recycle and Reuse, NASA Marshall Space Flight Center in Huntsville, Alabama. “Recycling and reuse could potentially reduce mass, increase mission flexibility, provide a path towards sustainable manufacturing, and produce on-demand spares.”
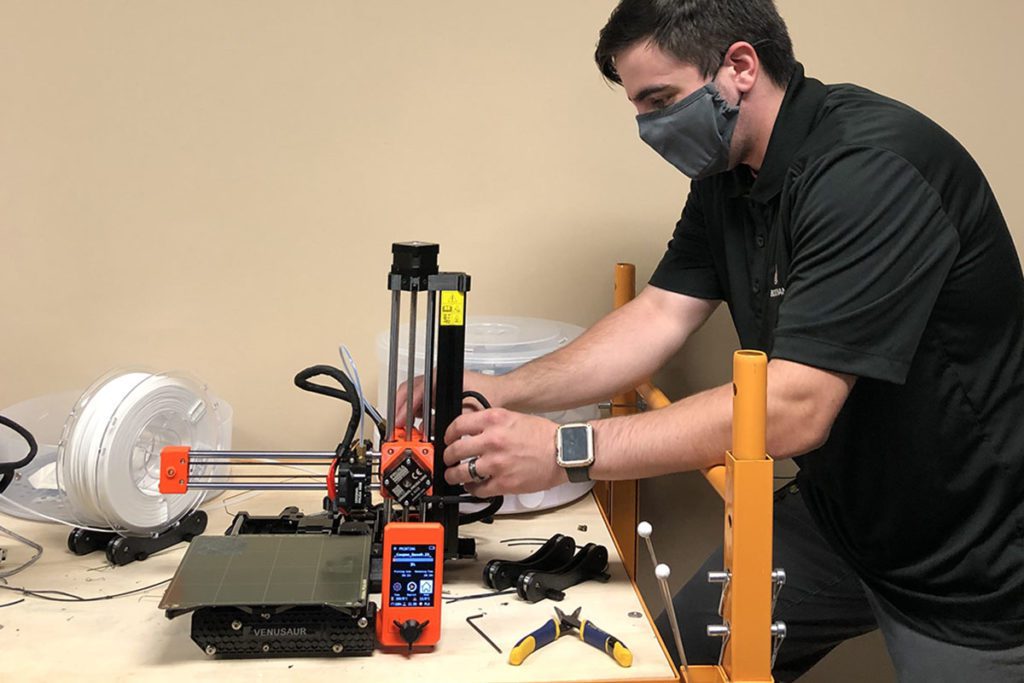
According to Blanchard, this is crucial for the conservation of medical equipment because they are frequently single-use items.
“If we can reprocess the same material several times for different applications through several recycling and re-manufacturing processes, without significantly losing its antimicrobial or physical properties, we will reduce weight, time, and the number of resupply missions,” Blanchard continued. “This would make future space missions safer and more feasible.”

The study that was started in 2018 will be expanded upon by the partnership between UNO and Copper3D. Initial grant funds allowed for the testing of antimicrobial 3D printing materials in microgravity. A second grant given out in 2019 assessed the viability of printing a number of medical equipment in 3D under zero-gravity.
In addition to working with businesses and universities through CopperX, their Open Innovation Unit, Copper3D also solves unusual difficulties in harsh locations like space exploration sites. A recent CopperX initiative gave underdeveloped nations with limited access to clean water copper ion exchangers, a technology used to treat pathogen-free drinking water.
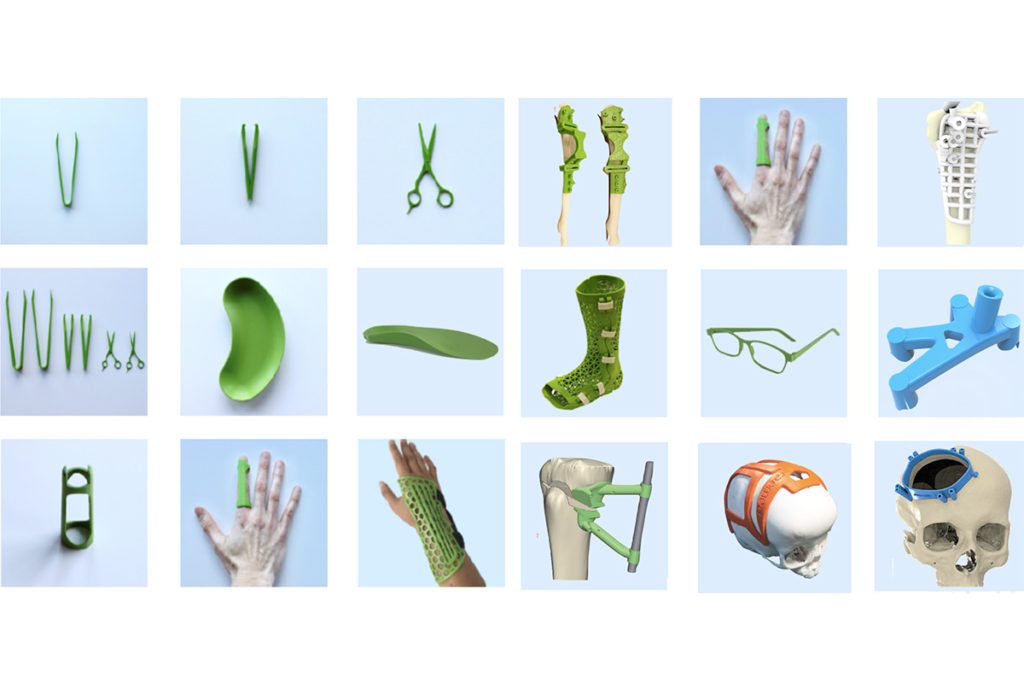
“For our team at Copper3D, it is tremendously relevant and exciting to see how antimicrobial 3D printing technology, which we pioneered in 2017, has quickly found multiple areas of impact and development of solutions,” said Daniel Martínez, Co-Founder and Director of Innovation at Copper3D.
“We sincerely believe that Copper3D technology can prevent infections and save lives on a global scale, and we are about to prove that on an interplanetary scale as well.”
Here at 3DAPAC, we’re proud to be able to supply Copped3D materials for you to use in your additive manufacturing solutions. Check out our shop online or contact us for a custom solution to your 3D Printing problems!